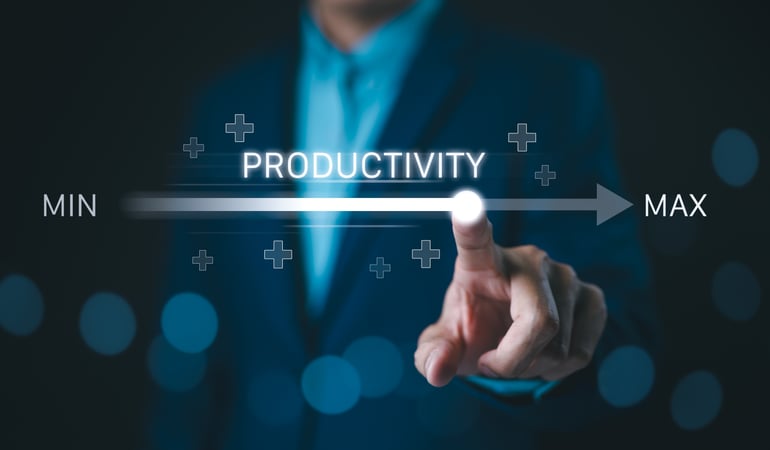
Boosting Technician Productivity: The Role of Mobile FSM Solutions in the Refrigeration Sector
Maintaining productivity is a top priority in the world of refrigeration services. Technicians often face the pressure of completing service tasks efficiently while ensuring the highest quality standards are upheld. Mobile Field Service Management (FSM) software solutions have emerged as a game-changer, offering relief from this constant pressure. Let's explore how these tools revolutionise productivity for refrigeration technicians.
Seamless Access to Real-Time Information
Imagine this scenario: A refrigeration technician arrives at a site only to discover they need additional documentation or details about the system they are servicing. This delay could stretch into hours with traditional paper-based systems, reducing productivity and causing customer dissatisfaction. Mobile FSM software eliminates this bottleneck by providing instant access to critical information.
Technicians can directly access job details, service histories, schematics, and troubleshooting guides from smartphones or tablets. This real-time information allows them to assess and execute tasks efficiently, minimising downtime caused by incomplete data or knowledge gaps.
Benefits:
- Reduced back-and-forth communication between the field and office.
- Faster service times due to immediate access to asset records.
- Improved confidence and control over tasks, boosting morale and efficiency.
Enhanced Scheduling and Route Optimisation
Efficient scheduling and routing are significant productivity challenges in the refrigeration sector. Traditional methods often result in inefficient travel routes and double bookings. Mobile FSM software uses advanced algorithms to optimise these processes.
Features like drag-and-drop scheduling allocate jobs based on technician skill sets, availability, and location. With integrated vehicle tracking, dispatchers can see which technician is closest to an urgent job, reducing response times. This optimisation ensures technicians spend more time servicing equipment and less on the road.
Key Advantages:
- Significant reduction in travel time.
- Higher first-time fix rates with appropriate allocation of skilled personnel.
- Better utilisation of resources, leading to increased productivity.
Automated Alerts and Notifications
Timeliness is crucial in refrigeration maintenance, especially when dealing with systems that preserve perishable goods. Delays can have catastrophic financial and operational consequences for clients. Mobile FSM software features automated alerts and notifications, keeping everyone informed throughout the service lifecycle.
Technicians receive reminders about upcoming jobs and notifications of schedule changes or urgent requests. This functionality ensures they are always in the loop, leading to fewer missed appointments and better-prepared service calls. Additionally, customer alerts notify clients of technician arrival times, enhancing transparency and satisfaction.
Impact on Productivity:
- Fewer missed or delayed appointments.
- Efficient job management, allowing technicians to focus on technical tasks.
- Enhanced client relationships, reducing repeat visits caused by miscommunication.
Paperless Workflows for Efficient Reporting
Gone are the days of paperwork causing unnecessary delays and errors. Mobile FSM solutions support paperless workflows, enabling technicians to digitally complete and submit service reports, safety checklists, and maintenance records. This instant documentation reduces administrative overhead and ensures compliance with industry standards.
Technicians can complete digital forms on-site and link them directly to the job record, simplifying compliance with regulations like F-Gas documentation and ensuring every service is accurately documented.
Advantages:
- Faster report completion with fewer manual errors.
- Easy retrieval of compliance records for audits.
- Reduced administrative workload, allowing technicians to take on more jobs daily.
Inventory and Parts Management on the Go
Refrigeration technicians often need more time due to available or misplaced parts. Mobile FSM solutions tackle this issue with real-time inventory management. Technicians can check part availability before arriving on-site and request necessary items through the app.
Integration with stock control systems alerts managers to low inventory levels, improving resource planning.
Results:
- Minimised downtime caused by part shortages.
- Improved first-time fix rates as technicians are fully prepared.
- Enhanced inventory forecasting and planning for managers.
Data-Driven Decision-Making with Reporting and Analytics
Businesses can track key performance metrics like job duration, first-time fix rates, and response times. By analysing this data, they can identify areas for improvement and implement targeted training or resource allocation strategies. This data-driven approach boosts productivity and ensures long-term service quality.
Long-Term Benefits:
- Continuous performance monitoring for technicians.
- Proactive maintenance strategies informed by historical data.
- Streamlined operations refined through ongoing analysis.
In a sector as demanding as refrigeration, where even minor inefficiencies can lead to significant financial loss, mobile FSM solutions are indispensable. These tools empower technicians by automating routine tasks, optimising scheduling, and providing real-time access to essential data, giving them control over their work and operations. As technology evolves, investing in robust FSM software will be even more crucial for refrigeration service companies looking to stay ahead of the competition.
Take control of your refrigeration service operations today. Discover how FSM software can transform your business and experience the benefits of seamless communication, real-time updates, and unparalleled efficiency. Ready to elevate productivity and streamline operations? Explore your options and book a demo to see these solutions in action.