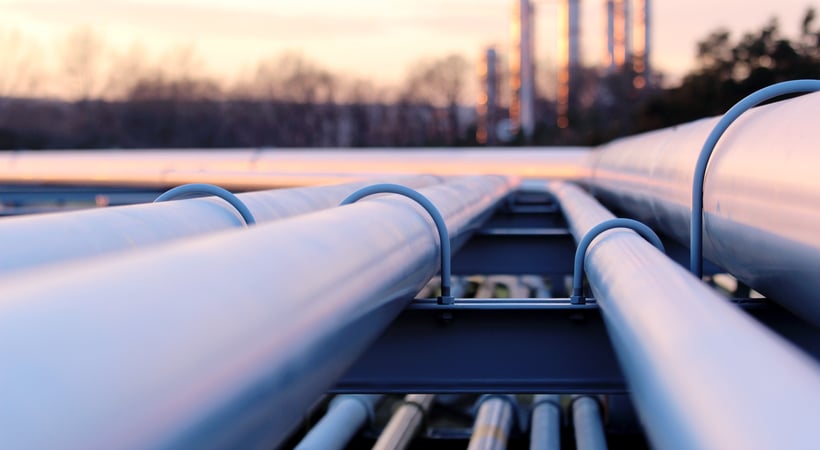
Embracing the Cloud: Revolutionising Gas Engineering with Cutting-Edge Technology
As time goes by, new trends and innovations emerge, playing a crucial role in shaping the gas engineering sector. These trends constantly evolve, making it essential to stay up to date with the ones significantly impacting the sector's development.
What is the current trend that is defining the gas engineering sector?
Amid all the technological advancements and innovations, the fundamental element of most of them is cloud-based solutions. Cloud software offers on-demand access to solutions from any location. This improves the efficiency of your field services and allows you to access the software from anywhere and at any time you need.
What are the benefits of Cloud-Based Solutions?
Cloud-based gas engineering software is explicitly designed for the gas engineering industry. It provides field technicians with access to critical job details and customer records from any internet-enabled device. This increased accessibility fosters better collaboration and communication among team members, leading to more efficient, timely, and effective service delivery. Moreover, with the cloud enabling real-time updates and data backups, high data integrity is ensured, which is crucial in dealing with the shifting and stringent regulatory compliance requirements.
What does cloud-based gas engineering software enable?
Cloud-based software has transformed gas engineering and field service operations, making several practical changes.
Workflow Automation
One of the most transformative areas has been automating repetitive tasks such as scheduling, dispatching, and invoicing. Gas engineer software can use intelligent algorithms to optimise the route and assign resources to ensure the best services are delivered within the shortest time possible. Automating these tasks enhances operational efficiency and significantly reduces the potential for human error.
Empowering Customers Through Self-Service Portals
In today's market, customer focus is of prime importance. It is crucial to provide a hassle-free and transparent way for customers to handle their interactions. One of the features of some gas engineer software platforms is the self-service portal. This portal enables customers to make an appointment, track the progress of a job, and even view previous service histories. This level of empowerment and transparency significantly boosts customer satisfaction and loyalty.
Mobile Accessibility: Bridging the Field and Office
The shift from traditional on-premises systems to cloud-based solutions has opened a new frontier regarding mobile accessibility. With the help of a mobile application, users can now update their job information, schedules, and customer details while on the go. This has enabled better real-time communication between field technicians and back-office teams, significantly enhancing overall productivity and operational efficiency.
A Practical Example: Streamlining Job Scheduling
Consider an improved method of job scheduling and assignment facilitated by cloud-based systems. With this method, office teams can easily assign tasks to field engineers who receive automated alerts on their mobile devices. This streamlined approach demonstrates the system's efficiency, reducing the time and effort required for administrative tasks and allowing engineers to concentrate on their essential duties.
The Role of IoT (Internet of Things) in Advancing Gas Engineering
One key benefit of cloud-based engineering software is that it allows systems to connect with the Internet of Things. This means that you can integrate diagnostic and monitoring equipment, such as smart sensors and meters, into your system. With this setup, you can collect real-time equipment performance data, laying the groundwork for proactive maintenance and issue resolution.
Revolutionising Maintenance and Diagnostics
Cloud-based gas engineer software leverages IoT to detect and prevent issues, reducing downtime and maintenance costs. This proactive approach is further enhanced through:
Predictive Maintenance: Foreseeing the Unseen
Predictive maintenance algorithms use historical data and usage patterns to anticipate equipment failures. They allow maintenance tasks to be scheduled in advance, prevent breakdowns, minimise maintenance costs, and extend the lifespan of gas appliances.
Remote Diagnostics: Minimising Response Times
Diagnosing and resolving issues remotely has revolutionised troubleshooting equipment faults, performing updates, and calibrating systems without needing on-site visits. With access to remote systems, you can reduce operational costs and improve results by speeding up response times, enhancing customer satisfaction.
The Road Ahead: Challenges and Opportunities
As the industry evolves, adopting these technologies becomes less of an option and more of a strategic imperative. Businesses that embrace cloud-based solutions and IoT benefit from improved operational efficiencies, reduced costs, and enhanced customer satisfaction. Moreover, predicting and preventing equipment failures through advanced diagnostics and predictive maintenance can significantly extend asset lifespans, offering substantial long-term savings.
The journey towards digital transformation is full of possibilities, but it also comes with obstacles. These include data security concerns, the need for skilled personnel to manage and interpret IoT data, and the initial investment required for technology adoption. Nevertheless, the potential benefits of digital transformation far outweigh these challenges, making it essential for businesses to navigate them strategically.
If you are looking to acquire or change your gas engineering software, make sure to talk to our experts about how Joblogic gas engineering software can help your business.