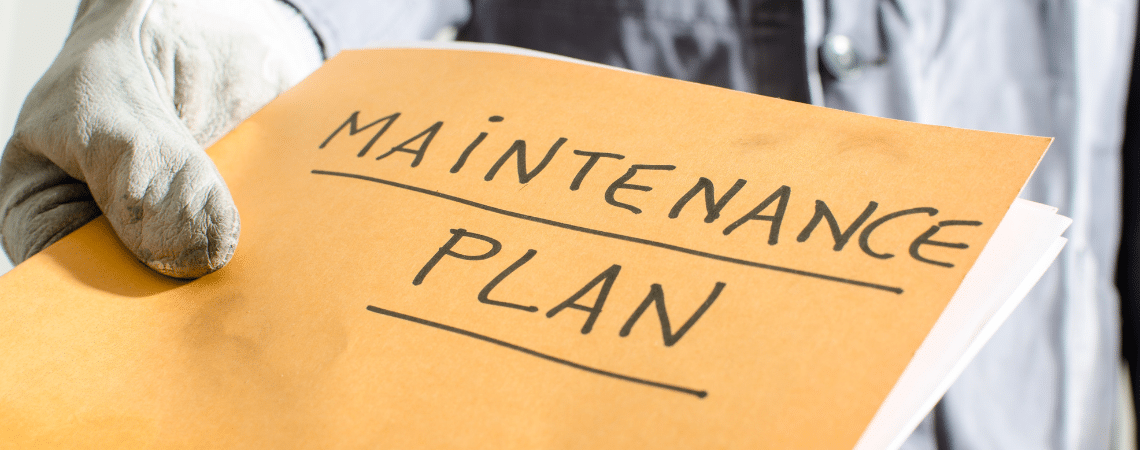
How to build a planned preventative maintenance schedule that doesn’t get in the way of your other maintenance tasks
When it comes to conquering the challenges of facilities management, one of the biggest issues is making sure that all assets and equipment maintain all maintenance requirements to ensure functionality and reduce downtime.
60% of businesses are focused solely on reactive maintenance, where an engineer is sent out to look at an asset after errors or faults have been reported. This is essentially the firefighting approach to maintenance. Your team will be spending all their time focused on repairing assets only when issues get reported. This approach is the bare minimum of how facilities managers should be managing asset maintenance, but there is a better approach that will result in:
- Lower maintenance costs
- Extended equipment lifespans
- Improved operational efficiency
How is this achieved? It’s done through planned preventative maintenance, or PPM for short. A PPM schedule is an approach that focuses on finding potential issues before they progress into problems, that either poses a health and safety risk or end up causing downtime for the equipment. By scheduling regular check-ups and maintenance for assets, you can improve the efficiency of your asset maintenance schedules in a way that will be noticeable to the wider business.
What does a PPM schedule look like?
There are a variety of ways to configure your PPM schedule. Depending on the type of assets you’re using, you may want to use a combination of each of these approaches.
Approach 1 – Time-based PPM
Time based PPM is the simplest form of PPM. Every (X) months you’ll send an engineer out to the asset to check its performance. How regular the checks are will be based on recommendations of your engineers, and the asset type that’s being maintained.
Approach 2 – Usage-based PPM
If a piece of equipment is used with high frequency, then the best approach may be to schedule maintenance based on the amounts it’s been used. For instance, with a car this would entail that maintenance would happen after X many miles had been driven. This type of of PPM schedule can be the most difficult to implement as each type of asset will have different use cases, and you’ll need to be able to track the usage of the asset through your asset register in some form.
This approach may work best when combined with time-based PPM, as you can do smaller checks at regular intervals, and then when the usage levels have been hit, a more thorough maintenance check can be booked in.
Approach 3 – Condition-based PPM
It’s possible to argue that this approach isn’t true PPM, but is just a minor variation of reactive maintenance, as condition-based PPM is based around you looking out for indicators of potential failure. This could be excessive vibrations from equipment or noticeable noises that otherwise shouldn’t be expected from the asset. Once a condition has been noticed then a maintenance visit can be scheduled.
Approach 4 – SFG20 schedules
Perhaps the best way to maintain assets is to adopt the SFG20 PPM schedule. SFG20 is the industry standard for building maintenance specifications and provides over 1200 maintenance schedules for over 70 different types of equipment and assets.
SFG20 schedules not only provide you with a breakdown of when each type of asset should be scheduled for maintenance, but it will provide you with a range of indicators as to what sort of maintenance is needed via colour coding:
- Red – Statutory (Legal compliance)
- Pink – Mandatory and business critical (Organisational compliance)
- Amber – Optimal (Best practice)
- Green – Discretionary (non-critical maintenance)
Why do you need a PPM schedule?
Switching to preventative maintenance schedules brings about a range of benefits for your business. These include:
a. Lower maintenance costs
Studies have shown that reactive maintenance approaches cause maintenance costs to be 30-40% higher when compared to PPM schedules. Not only does it cost more in literal repairs, but the costs of a reactive approach ripple throughout other parts of the business as well. Emergency repairs means unplanned downtime, which means a loss of productivity, which can massively affect the bottom line of a business.
b. Extended asset lifespans
Using PPM schedules means that you can find and fix potential issues before they escalate. With routine inspections and making sure basic maintenance is done, such as lubricating moving parts or replacing worn-out components, means that you’ll be able to extend the lifespan of the equipment. This doesn’t just prevent downtime and ensure productivity remains high, but it also means you spend less money replacing assets over time, saving money in the short and long-term.
c. Enhanced operational efficiency
With a PPM schedule in place, you’ll be able to minimise unexpected equipment failures, which will help you to avoid downtime that can be costly for the business and impact not just productivity, but potentially customer satisfaction as well.
What’s the best way to build a PPM Schedule?
Whatever way gets used as the basis of your PPM schedule, keeping to the schedule can be tricky. Utilising basic tools like excel documents and spreadsheets can cause confusion, as details and information can changes or get lost. Working through multiple software types can also create unnecessary duplication of work and administrative tasks.
To work around this, you need to invest in an all-in-one piece of software that allows you to efficiently schedule jobs, track job statuses, store asset lists and access information about assets from a mobile device. All of these (and much more) can be done with a Computerised Maintenance Management System (CMMS), sometimes referred to as job management software or PPM software.
With CMMS software in place, you’ll be able to fully track all your maintenance activities, the history of repairs, and create comprehensive reports that provide meaningful insights into your maintenance activities. This allows you to streamline your maintenance operations and make more informed decisions.
How do you ensure that your PPM Schedule doesn’t get in the way of other tasks?
The reality of any maintenance work is that you’ll still need to perform reactive tasks or handle other jobs that are separate from your PPM schedule. To ensure that these jobs still get done and your PPM schedule doesn’t take away from necessary emergency work, you need to make sure that your CMMS system is cloud-based so that the PPM schedule and reactive maintenance jobs can be updated in real-time. Your engineers can access job information, get alerted to when jobs are assigned or change via an app that syncs up to the CMMS whenever it’s connected to the internet. This means your team can focus their time on the priority tasks and jobs, and ensures that no job gets missed.