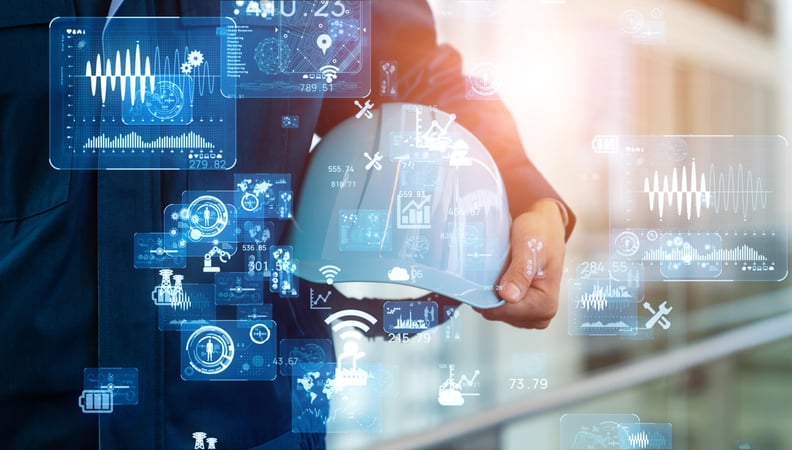
How the Internet of Things can help Maintenance
Predictive maintenance is a planned maintenance software approach that uses condition monitoring data and advanced analytics to identify the degradation of equipment before it breaks. This process is made possible with Internet of Things (IoT), which provides the necessary data to make accurate predictions.
What is the Internet of Things (IoT)?
The Internet of Things (IoT) is a system of interconnected devices that contain sensors, processing abilities, and connectivity that collects and exchanges data. In addition to traditional computing devices like laptops and smartphones, IoT devices can also include objects like cars, home appliances, and industrial machines.
We already use our smartphones to turn on our heating, close shutters, switch lights on, etc. So the concept of an interconnected device is not new. However, industrial companies who have generally relied on reactive maintenance are starting to see the value in moving to a proactive equipment maintenance model.
How Does IoT Relate to Predictive Maintenance?
Whether your business operates in manufacturing, automotive, aerospace, or any other industrial sector, chances are you have mechanical equipment that requires maintenance. Traditionally, planned preventative maintenance (PPM) has been used to maintain equipment, implementing scheduled maintenance tasks, such as oil changes and filter replacements, based on time or usage.
However, with the advent of predictive planned maintenance software and IoT, businesses can now monitor their equipment in real-time and detect potential problems before they occur. IoT devices used for predictive maintenance may include sensors, and actuators. These devices collect raw data, resulting in the following actions to ensue:
- A sensor will filter and transmit the data to a cloud-based platform. Here, data can be processed and analysed using machine learning software or maintenance staff who can review it manually.
- Actuators will detect a signal and will modify the machine’s physical output automatically.
How Can IoT Help My Business?
Uptime on assets and machines is crucial to the success of any business, particularly those in manufacturing or other industrial sectors. By using IoT devices for predictive maintenance, companies can increase operational efficiency, increase automation, and reduce downtime.
- Predictive Maintenance
- Real-time Data
- Performance Metrics
- Automatic Repair Recommendations
Predictive Maintenance
As mentioned, equipment uptime is essential for businesses. Assets that operate longer, with fewer failures, can lead to increased productivity and profitability. You’ll increase customer satisfaction and reduce the need for replacement parts and repairs.
IoT-based predictive planned maintenance software helps businesses by providing visibility into the performance and health of their assets. By analysing data collected by IoT devices, businesses can detect potential issues before they happen and take steps to prevent them.
What’s more, by collecting data on asset performance, businesses can identify trends and optimise their maintenance processes. For example, suppose a freezer in a supermarket or restaurant experiences a sudden drop in temperature during off-hours. In that case, this could indicate that the door has been left open or there is a problem with the cooling system. Subsequently, a technician would be dispatched to fix the issue before it leads to spoilage of goods.
Read our guide on anomaly detection and it’s importance within the field maintenance industry.
Real-time Data
Real-time data is essential for businesses to make informed decisions, providing a snapshot of what is happening at the present moment. For example, if you’re an air conditioning maintenance technician, tracking temperature changes in real-time can help you troubleshoot issues faster and improve the efficiency of your service calls.
Sometimes, raw data that hasn’t had further analysis is practically worthless as it needs to be processed and analysed to be of any use. This is where many businesses struggle, as they don’t have the time, resources, or expertise to make sense of data collected by their IoT devices. Cloud-based and machine learning solutions can help with this, as data can be transmitted and processed in real-time, giving businesses visibility and unique insights into their equipment 24/7.
Performance Metrics
Businesses need to track a variety of performance metrics to ensure their assets are running smoothly. With IoT devices, companies can automatically collect data on a wide range of metrics, including temperature, humidity, vibration, pressure, and flow rates. Without knowing what performance metrics to track, businesses can’t hope to improve the efficiency of their assets.
For manufacturers, machine vibration monitoring can help to identify issues before they escalate. Machines have various components that generate their own vibration frequency, overall creating a smooth flow that ensures machines operate normally. When a component fails, these vibration frequencies can change and become erratic. By pinpointing these changes, you can schedule maintenance before the part fails and causes downtime.
When you’re meeting or exceeding your equipment’s performance metrics, this is a good indication that your predictive maintenance program is working as intended.
Automatic Repair Recommendations
IoT devices can be highly effective in collecting information, but interpreting that information can be difficult. Thus, many businesses hire additional technical staff or rely on service providers to give them recommendations on troubleshooting an issue. This process is often time-consuming and quite expensive.
However, a new generation of IoT-based predictive planned maintenance software solutions have emerged that automatically uses machine learning algorithms to diagnose problems and provide repair recommendations. These solutions don’t rely on human input so they can provide recommendations much faster, saving the need on hiring new staff.
For a real-life example of repair recommendations put in practice, we need to look no further than Sandvik, an engineering group specialising in tooling systems. After Sandvik partnered with Microsoft, cutting equipment with sensory abilities were produced for various industries. These tools combined data computation, analytics, and artificial intelligence to recommend predictive maintenance schedules to optimise machines.
So what does this mean for companies who adopt this technology? As long as the sensors are kept clean and calibrated, they will continue to work effectively and provide repair recommendations.
How Can Joblogic Help Me Put IoT in Place Within My Business?
Joblogic’s all-in-one management software is the perfect solution for businesses wanting to improve their predictive maintenance programs with IoT. Once your IoT devices are connected, data can be transmitted to Joblogic, giving your field service staff and back-office visibility into your equipment round the clock.
Having access to real-time data on equipment means that your team can identify and resolve issues faster, improving the efficiency of your business. And with Joblogic’s flexible scheduling system, you can also easily schedule and track maintenance appointments, ensuring your assets are continually operating at peak performance.
Get in touch with our team today if you’re ready to improve your predictive maintenance program with Joblogic. We provide a free demo of our software, so you can see firsthand how Joblogic can benefit your business.