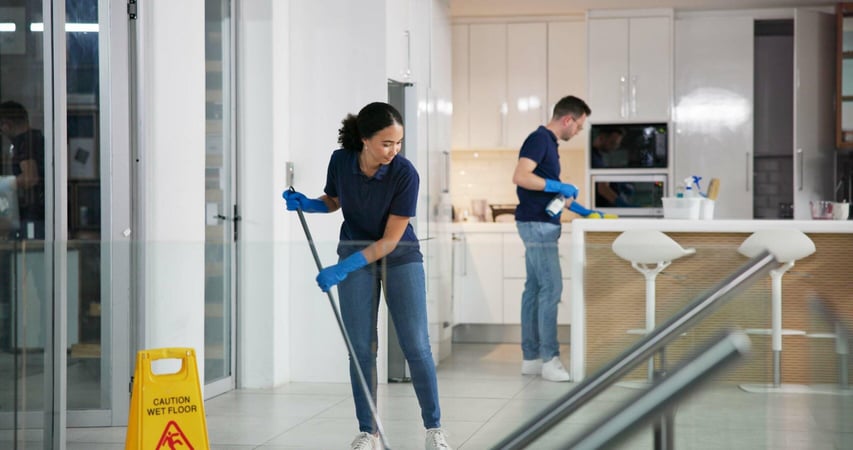
The Future of Building Maintenance - Embracing Digital Work Order Management
The building maintenance industry has traditionally relied on manual processes, paperwork, and reactive approaches to managing work orders and maintenance schedules. However, as the complexity of managing extensive facilities grows and expectations for efficiency rise, the sector is increasingly moving toward digital solutions. Among these innovations, digital work order management systems stand out as a crucial tool for service and facilities managers responsible for keeping operations running smoothly.
This blog explores why digital work order management is the future of building maintenance and how it benefits service and facilities managers in their quest for efficiency, improved productivity, and cost savings.
The Evolution of Building Maintenance
The field of building maintenance has experienced a remarkable transformation over the years. Once characterised by a broadly reactive and paper-driven approach, maintenance today demands a more proactive, data-driven, and streamlined methodology. Let's look at this evolution.
Past: Reactive Maintenance
Traditionally, maintenance teams responded to issues only after they occurred. This process often involved extensive paperwork, manually logging requests, and coordinating tasks through phone calls or in-person communication. This approach led to inefficiencies, such as delayed responses, unorganised record-keeping, and missed maintenance opportunities that could have prevented more significant problems.
Present: The Rise of Digital Solutions
With the advent of digital technologies, building maintenance has become more sophisticated. Today, service and facilities managers are expected to handle a growing number of assets, locations, and systems—all while meeting strict safety and compliance standards. This has led to the adoption of digital work order management systems designed to streamline operations, reduce errors, and improve overall maintenance efficiency.
However, many organisations still face challenges in their day-to-day operations:
- Manual tracking of work orders is often slow and laborious, leading to delays in task completion.
- Keeping track of numerous tasks across different sites becomes increasingly complex without a centralised system.
- Technicians and managers may struggle to sync due to outdated communication methods.
- Lack of real-time tracking and reporting makes optimising long-term asset management and performance hard.
These challenges highlight the need for a more integrated, scalable solution, which digital work order management can provide.
Why Digital Work Order Management is the Future
Digital work order management systems are revolutionising building maintenance. Automating various aspects of the maintenance process has enabled facilities and service managers to overcome traditional challenges and future-proof operations.
Streamlining Operations
One key benefit of digital work order management is its ability to streamline operations. By automating work order creation, scheduling, dispatching, and tracking, these systems eliminate the need for manual intervention at every step. This automation leads to quicker response times, more efficient task execution, and fewer errors, contributing to smoother day-to-day operations.
For instance, service managers can use digital platforms that automatically assign tasks based on technician availability and proximity instead of manually tracking work orders on paper or in spreadsheets. This ensures that work orders are addressed in the most efficient manner possible.
Improved Efficiency and Productivity
A well-implemented digital work order management system improves the efficiency and productivity of maintenance teams. Technicians can access real-time information about work orders via mobile devices, allowing them to view job details, upload photos, update statuses, and communicate with managers in the field. This real-time access reduces downtime, improves accuracy, and ensures tasks are completed faster.
Additionally, automated notifications alert technicians and managers about critical updates, such as when a work order is completed or any urgent issues requiring immediate attention. This keeps everyone in the loop and eliminates the need for constant follow-ups.
Data-Driven Decision-Making
Digital systems collect vast amounts of data, which can be analysed to make informed, data-driven decisions. Service and facilities managers can leverage this data to track key performance indicators (KPIs) such as response times, completion rates, and recurring issues. With this insight, they can identify trends, predict maintenance needs, and make strategic decisions to improve future performance.
For example, data from work orders can help managers recognise patterns in equipment failure, allowing them to implement preventive maintenance measures that reduce unplanned downtime and extend the life of critical assets.
Cost Savings
One of the most tangible benefits of digital work order management is cost savings. By streamlining processes, reducing administrative overhead, and enabling predictive maintenance, these systems help organisations minimise operational costs.
Preventive and predictive maintenance made possible through data analysis can significantly reduce the need for expensive emergency repairs. Additionally, automated scheduling helps optimise resource allocation, ensuring that technicians are dispatched efficiently and reducing unnecessary labour costs.
Key Features of Digital Work Order Management Systems
The effectiveness of a digital work order management system lies in its features. Below are some key functionalities that make these systems indispensable for service and facilities managers in the building maintenance sector.
Real-Time Tracking and Visibility
Digital work order systems provide real-time visibility into the status of all work orders. Managers can monitor each task from the moment it is created to its completion, ensuring complete transparency across the maintenance operation. This makes prioritising urgent tasks easier, avoiding missed deadlines, and ensuring that all maintenance activities are completed on time.
Mobile Access for Technicians
Most modern work order systems include mobile apps allowing technicians to access job details, update work statuses, and communicate with the office in the field. This mobility reduces delays, as technicians can receive new work orders instantly, submit real-time updates, and even upload photos or reports directly from their smartphones or tablets.
Automated Scheduling and Dispatching
Automated scheduling is a game-changer for service and facilities managers. With a digital system, work orders can be automatically assigned to technicians based on location, availability, and skillset. This ensures that tasks are completed efficiently, helps reduce downtime, and avoids unnecessary travel for technicians.
Centralised Communication
Digital work order management systems provide a centralised platform for communication between service managers, technicians, and clients. Instead of relying on emails, phone calls, or text messages, all communication can be tracked within the system, ensuring that everyone stays on the same page and reducing the risk of miscommunication or lost information.
Analytics and Reporting Tools
Advanced digital work order management systems come with built-in analytics and reporting tools that provide insights into the maintenance operation's overall performance. Managers can use these tools to generate reports on work order completion rates, technician performance, asset reliability, and more. This data is invaluable for identifying areas for improvement and making informed, strategic decisions.
Benefits for Service Managers and Facilities Managers
For service and facilities managers, adopting digital work order management systems offers a range of advantages that directly address the common challenges faced in building maintenance.
Greater Control Over Operations
Digital work order systems provide service managers complete visibility into the maintenance process. From tracking individual work orders to monitoring the overall workload, managers can make more informed decisions and quickly address any issues.
Improved Customer Satisfaction
Faster response times and more accurate updates lead to improved customer satisfaction. Clients are informed about their requests' status, and service managers can easily track and prioritise high-importance tasks - this increased transparency results in better client relationships and a more professional service experience.
Reduced Paperwork and Admin Time
With digital work order management, much of the administrative burden is automated. Service managers no longer need to manually enter data, track paperwork, or follow up on work orders. This reduction in paperwork frees up time for managers to focus on more strategic tasks, such as optimising processes and improving team performance.
Scalability
As organisations grow and take on more assets or locations, digital work order management systems offer scalability. These systems can handle increasing work orders without becoming overwhelmed, ensuring that operations remain smooth even as the business expands.
Proactive Maintenance
By leveraging data from past work orders, managers can transition from a reactive to a proactive maintenance approach. This enables preventive maintenance that reduces downtime and extends the lifespan of assets, ultimately leading to long-term cost savings.
The shift to digital work order management is more than just a trend - it's a critical step toward the future of building maintenance. Service and facilities managers who embrace this technology can look forward to more efficient operations, improved communication, better decision-making, and significant cost savings. As the industry continues to evolve, those who adopt digital solutions will be well-positioned to stay ahead of the curve and meet the growing demands of building maintenance in the modern era.