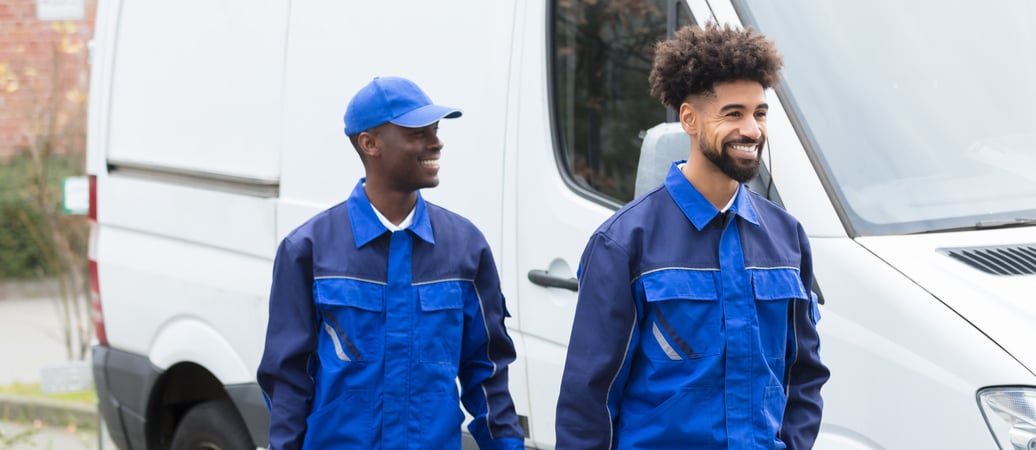
The role of field service management software in meeting the challenges of multi-site asset management
If you're responsible for multiple sites, several challenges can emerge that can be difficult to overcome without proper planning and coordination. The challenges can be varied, but often, every individual responsible for multi-site asset management faces a core set of challenges. To help you overcome these challenges, we've provided an overview of the most prevalent issues and, most importantly, how you can approach solving them.
Challenge 1: Communication and collaboration
When working across multiple sites, you'll often deal with different teams, departments, and people daily. So many other groups of people working across various sites can lead to a compartmentalisation effect where everyone ends up working in their silos, separate from everyone else in the organisation, which leads to gaps in communication and vital information falling through the cracks.
The Solution:
You'll need to use centralised communication platforms and collaborative tools to minimise the communication gaps across your multi-site teams. Informal calls or messages via WhatsApp can be convenient, but they rely on an informal process that results in people missing vital information. Instead, it would help if you were looking to build an internal strategy for communications that allows everyone to receive the same updates, use the same software systems, and access the same document repositories as everyone else. Ideally, this should all be done through as few software types as possible, which is why field service management software can be a great tool to overcome communications challenges, as it gives you access to a wide range of tools that can be used for communications to both your team members and your customer base.
Challenge 2: Data synchronisation and accuracy
When working across multiple sites, maintaining up-to-date and accurate data with all the information your team needs can be incredibly challenging. Sites can operate on different processes, procedures, and software, creating a situation where field engineers will be forced to input information multiple times, which means somewhere along the line, information and data won't be inputted where they need to be.
The Solution:
The easiest way to resolve data synchronisation and inaccuracy issues is to ensure that every site works from the same asset management systems. This will enforce procedures that everyone can work from and provide all the information you need is in place. On top of this, if you can get a cloud-based asset management system, data will be able to be synced up in real time if your team members' mobile devices are connected to the internet (and if they're not, the data will update as soon as they get a stable connection).
Challenge 3: Resource allocation
Multiple sites with their own set of specific assets mean that each site will have a set of requirements that other sites won't. This can cause problems with ensuring the right resources (whether materials that need to be stored on-site or personnel with the right skillsets are allocated to the right jobs) are assigned to the correct site.
The Solution:
Through the correct use of software, you can ensure you have the proper people and materials available for asset management jobs. Job management software can enable you to allocate the correct individuals with the relevant skill sets and certifications for jobs to maintain assets, and stock control systems that your team can access on their mobile devices to track what parts have been used, enable you to keep on top of how much of any given part is available at a site, allowing you to purchase replacements before you run out of stock.
With the correct reporting set up in place, you can even look at data related to the jobs that have been completed to identify what changes to how you operate need to be made at an operational level. Combined with the job management and stock control software, you can allocate your resources most efficiently.
So many software types, though, can lead to data synchronisation errors, as we discussed above. So, ,you should always use a single piece of software that offers all the features we've just discussed.
Challenge 4: Security and access control
With multiple sites, your team of field engineers will need to be able to access information from wherever they are, which means your database is accessed from various locations across a range of different devices (often ones that the engineer already has and you have no control over). As information about asset performance can be sensitive to allowing sites to fully function, it's vital that your data is secure to void any potential legal and operational issues.
The Solution:
Maintaining data security across your company when you have a field team working across multiple sites can be achieved by ensuring the software you use for asset management and job management has a series of built-in security features. Be on the lookout for:
- The ability to set up two-factor authentication to ensure access to software and mobile apps is limited solely to authorised individuals.
- The capacity to use password patterns on mobile apps to allow for easy but secure login attempts to access the information they need to complete the job.
- Limiting what your users can and can't see based on their permissions. For example, your engineers will need to access detailed notes on every asset, but there's no reason your general handyman and maintenance team need to see the exact details.
Challenge 5: Maintenance and repairs
Ensuring that assets across multiple sites are properly maintained can be difficult. Not only do each set of assets have unique requirements as to who can maintain and fix any issues that arise, but you need to be able to distribute the jobs from a single centralised location whilst keeping track of which team member is where so that other jobs become known you can make sure the nearest person with capacity is assigned the job. You also have the issue of how you can best schedule preventative maintenance jobs into the schedule so you're not just reactively acting to problems as they arrive.
The Solution:
You must ensure you have a proper CMMS, job management or maintenance software system. This will guarantee that you can assign the correct people to jobs as they emerge (for example, assigning an engineer with the relevant qualification to work on a specific asset). The job tracking features in these software types also mean you can see where your team members are and assign them maintenance jobs during the day to ensure tasks are completed quickly.
Ideally, your software should allow you to import SFG20 schedules into the system so that you can easily set up preventative maintenance tasks that are best practices for every type of asset that you're responsible for maintaining.
Consider how your software functions when working with subcontractors outside your organisation. Does it allow you to monitor their costs and purchase orders? If not, then you should consider switching systems.
As you can see, the core of multi-site asset management is ensuring you have the right software to properly manage the assets, jobs, and engineers you're responsible for. The ideal solution for your organisation is to use one piece of software that does everything you need.