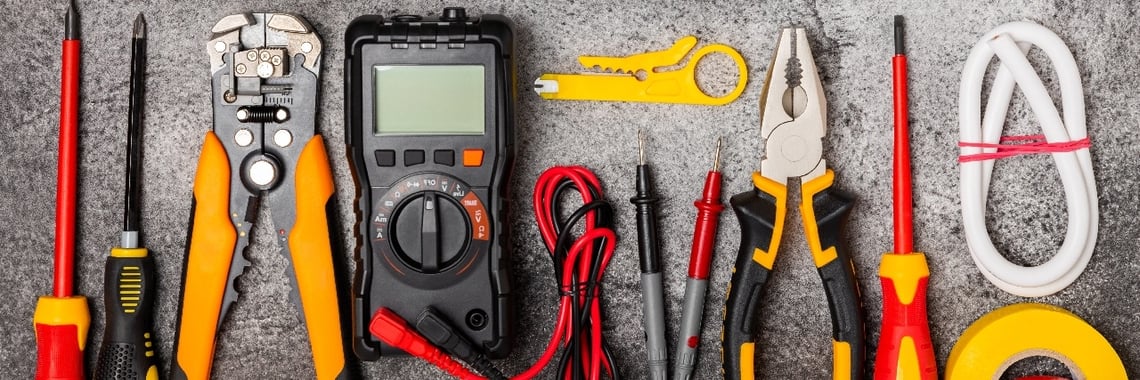
Top Strategies for Preventative Electrical Maintenance to Minimise Downtime
Reducing electrical maintenance downtime is critical in facilities management. Unplanned outages can halt operations, cause significant financial losses, and pose safety risks. Implementing a robust preventative maintenance strategy is essential for Service Managers and Contract Managers if you want to avoid these disruptions. But what is the best way to minimise downtime? Using our decades of experience working with electrical contractors and facility managers, we’ve identified the top strategies to minimise electrical maintenance downtime and want to share them with you so you can minimise downtime for yourself.
Understanding Preventative Electrical Maintenance
Preventative electrical maintenance is the proactive approach to maintaining electrical systems before issues arise. Unlike reactive maintenance, which deals with problems after they occur, preventative maintenance aims to anticipate and address potential failures. This approach not only minimises electrical maintenance downtime but also extends the lifespan of equipment, improves safety, and reduces overall operational costs.
Key Strategies for Effective Preventative Electrical Maintenance
To achieve the goal of reducing electrical maintenance downtime, Service Managers and Contract Managers should consider the following strategies:
Regular Inspections and Testing
Scheduled inspections are the cornerstone of preventative electrical maintenance. Regular checks help identify early signs of wear and tear, corrosion, or other issues that could lead to equipment failure. Key testing methods include:
- Thermal Imaging: Detects hotspots that indicate potential electrical faults.
- Insulation Resistance Testing: Assesses the integrity of wiring and insulation, preventing failures that could result in electrical maintenance downtime.
Implementation of CMMS (Computerised Maintenance Management System)
A CMMS is invaluable for managing preventative maintenance schedules, work orders, and asset data. Using a CMMS, Service Managers can streamline the scheduling of maintenance tasks, ensure compliance with safety regulations, and track asset health over time. This digital approach helps to significantly reduce electrical maintenance downtime by allowing proactive interventions before issues escalate.
Adopting Predictive Maintenance Techniques
Predictive maintenance leverages data analytics and IoT sensors to predict when equipment is likely to fail. By analysing trends in equipment performance, it is possible to address issues before they cause electrical maintenance downtime. This data-driven approach ensures that maintenance is performed only, when necessary, thereby reducing unnecessary disruptions and optimising resource use.
Training and Upskilling of Maintenance Teams
A well-trained maintenance team is vital for minimising electrical maintenance downtime. Ensuring that technicians are equipped with the latest knowledge and skills related to electrical systems and preventative maintenance techniques can lead to more accurate diagnostics and quicker repairs. Regular training sessions and certifications should be part of your preventative maintenance strategy.
Utilising CAFM and FSM Solutions
CAFM (Computer-Aided Facility Management) and FSM (Field Service Management) software provide real-time insights into the condition of your electrical assets. These platforms enable Service Managers to monitor systems remotely, schedule maintenance more effectively, and dispatch technicians with the right tools and information. By integrating CAFM and FSM software, you can achieve greater efficiency and reduce the risk of unexpected electrical maintenance downtime.
Automation and AI
Automation and AI play an increasingly important role in modern maintenance practices. Automated systems can schedule routine maintenance, generate work orders, and even provide diagnostics based on data from IoT sensors. AI can predict potential failures and recommend preventative actions, further minimising electrical maintenance downtime.
Overcoming Common Challenges
While the benefits of preventative maintenance are clear, several challenges can arise:
- Budget Constraints:
- The initial investment in preventative maintenance tools and technologies can be substantial. However, the long-term savings achieved by reducing electrical maintenance downtime often justify the expense.
- Resistance to Change:
- Gaining buy-in from stakeholders can be difficult. Demonstrating the ROI of preventative maintenance through case studies and data can help overcome this resistance.
- Data Management:
- Handling large volumes of maintenance data can be daunting. A well-implemented CMMS or FSM system can simplify data management and make interpreting and acting on the insights gained easier.
Preventative electrical maintenance is essential for minimising downtime, ensuring safety, and maximising the lifespan of your equipment. By implementing regular inspections, adopting a CMMS, embracing predictive maintenance, and leveraging technology, Service Managers and Contract Managers can significantly reduce electrical maintenance downtime.
Ready to take the next step? Book a demo of Joblogic’s CMMS and FSM software today and discover how we can help you streamline your maintenance processes, reduce downtime, and keep your operations running smoothly.